A simple innovative
high-performance system !
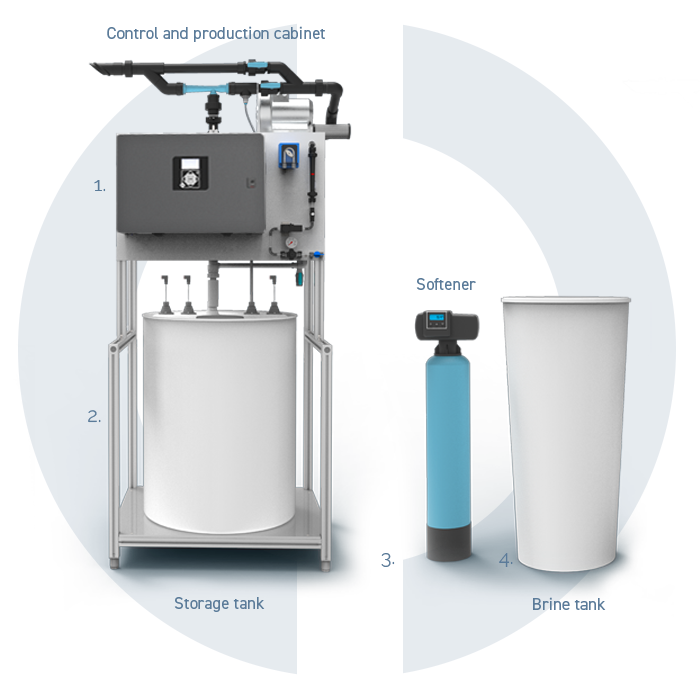
The system
is permanently supplied with mains water connected to a softener
(3)
(single or double depending on the model). The softened water will feed the brine tank
(4)
and the production circuit.
The brine tank (4) is fed by the softened water coming from the softener and allow blending with the salt previously poured at the bottom of the tank. The salt used must comply with one of the 4 standards thereafter : NF EN 973 Quality – NF EN 14805 Type 1 – NF EN 16401 Quality A – NF EN 16370
The dosing pump will inject the brine created at the entrance of the production circuit. This brine is mixed with softened water before entering the production cells.
The mixture obtained is injected into the production cells, through which an electric current flows. Based on the same principle as saltwater chlorination, the cells will create a naturally chlorinated solution: sodium hypochlorite.
The hydrogen lighter than air, generated during production, will be evacuated to the outside of the room with the help of a turbine for models with a production of more than 280 g/h. A hydrogen extraction system is available as an option on models 70 and 140 to complete the safety in the technical room.
The solution created is poured into a storage tank (2) secured by level sensors. The volume of the storage tank varies according to the model. Average concentration: 4 g/L of active chlorine.
The control and production unit (1) controls all the modules. The box controls the production reactor, manages the levels and the safety devices, allows programming the production periods in a simple and intuitive way thanks to a simple menu architecture.
Consult the parameters of your pools remotely be alerted thanks to the two communication systems installed on our devices: Real-time remote information: thanks to the insertion of a SIM card (not supplied) in the system, a set of administrators (pool managers) receive real-time alerts via SMS. Remote pool management with Connect Pro®: thanks to a simple connection to the local network, you can centralize all the information on the operating status of the installations.
A simple innovative
high-performance system !
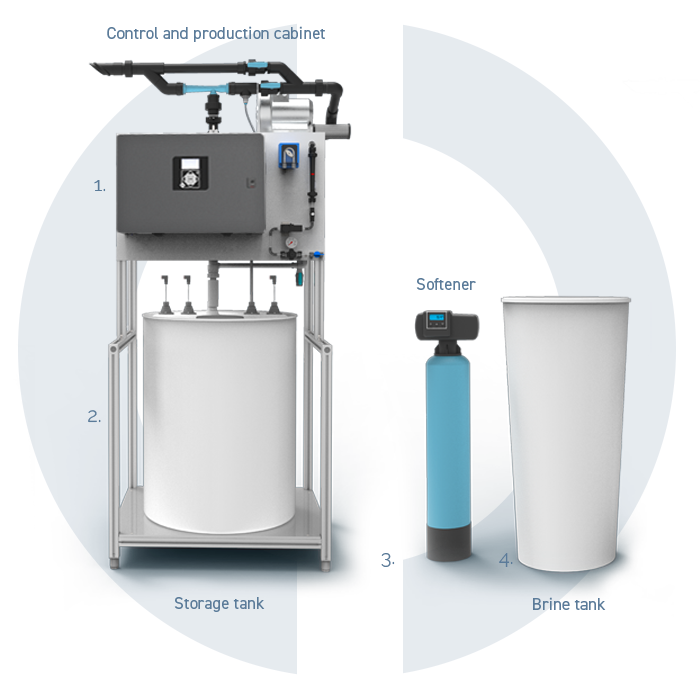
The system is permanently supplied with mains water connected to a softener (3) (single or double depending on the model). The softened water will feed the brine tank (4) and the production circuit.
The brine tank (4) is fed by the softened water coming from the softener and allow blending with the salt previously poured at the bottom of the tank. The salt used must comply with one of the 4 standards thereafter :
NF EN 973 Quality – NF EN 14805 Type 1 – NF EN 16401 Quality A – NF EN 16370
The dosing pump will inject the brine created at the entrance of the production circuit. This brine is mixed with softened water before entering the production cells.
The mixture obtained is injected into the production cells, through which an electric current flows. Based on the same principle as saltwater chlorination, the cells will create a naturally chlorinated solution: sodium hypochlorite.
The hydrogen lighter than air, generated during production, will be evacuated to the outside of the room with the help of a turbine for models with a production of more than 280 g/h. A hydrogen extraction system is available as an option on models 70 and 140 to complete the safety in the technical room.
The solution created is poured into a storage tank (2) secured by level sensors. The volume of the storage tank varies according to the model. Average concentration: 4 g/L of active chlorine.
The control and production unit (1) controls all the modules. The box controls the production reactor, manages the levels and the safety devices, allows programming the production periods in a simple and intuitive way thanks to a simple menu architecture.
Consult the parameters of your pools remotely be alerted thanks to the two communication systems installed on our devices: Real-time remote information: thanks to the insertion of a SIM card (not supplied) in the system, a set of administrators (pool managers) receive real-time alerts via SMS. Remote pool management with Connect Pro®: thanks to a simple connection to the local network, you can centralize all the information on the operating status of the installations.
A simple innovative
high-performance system !
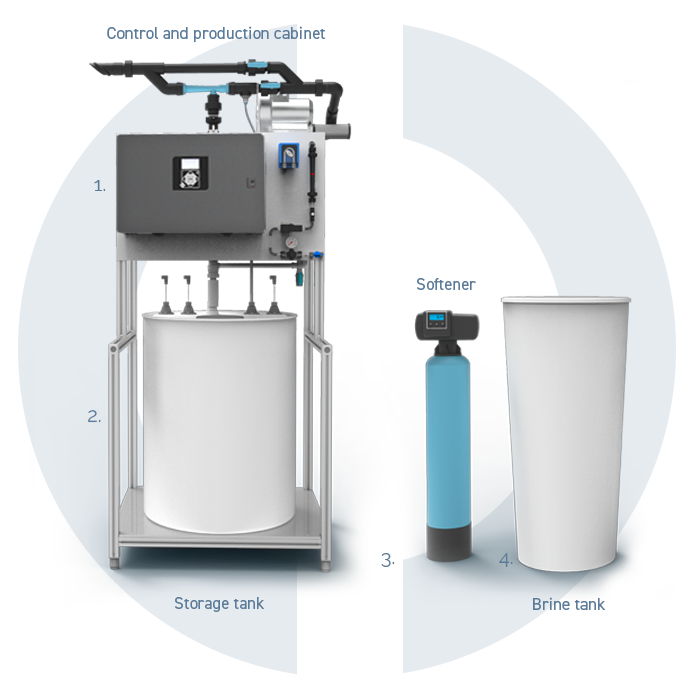
Consult the parameters of your pools remotely be alerted thanks to the two communication systems installed on our devices : Real-time remote information: thanks to the insertion of a SIM card (not supplied) in the system, a set of administrators (pool managers) receive real-time alerts via SMS.
Remote pool management with Connect Pro®: thanks to a simple connection to the local network, you can centralize all the information on the operating status of the installations.
Keep an eye
on your chlorine production !
iPOQLOR® is the ideal solution to these problems in the field !
REAL-TIME VIEW
OF YOUR DEVICE’S
VARIOUS
parameters
HISTORY
of data and alarms
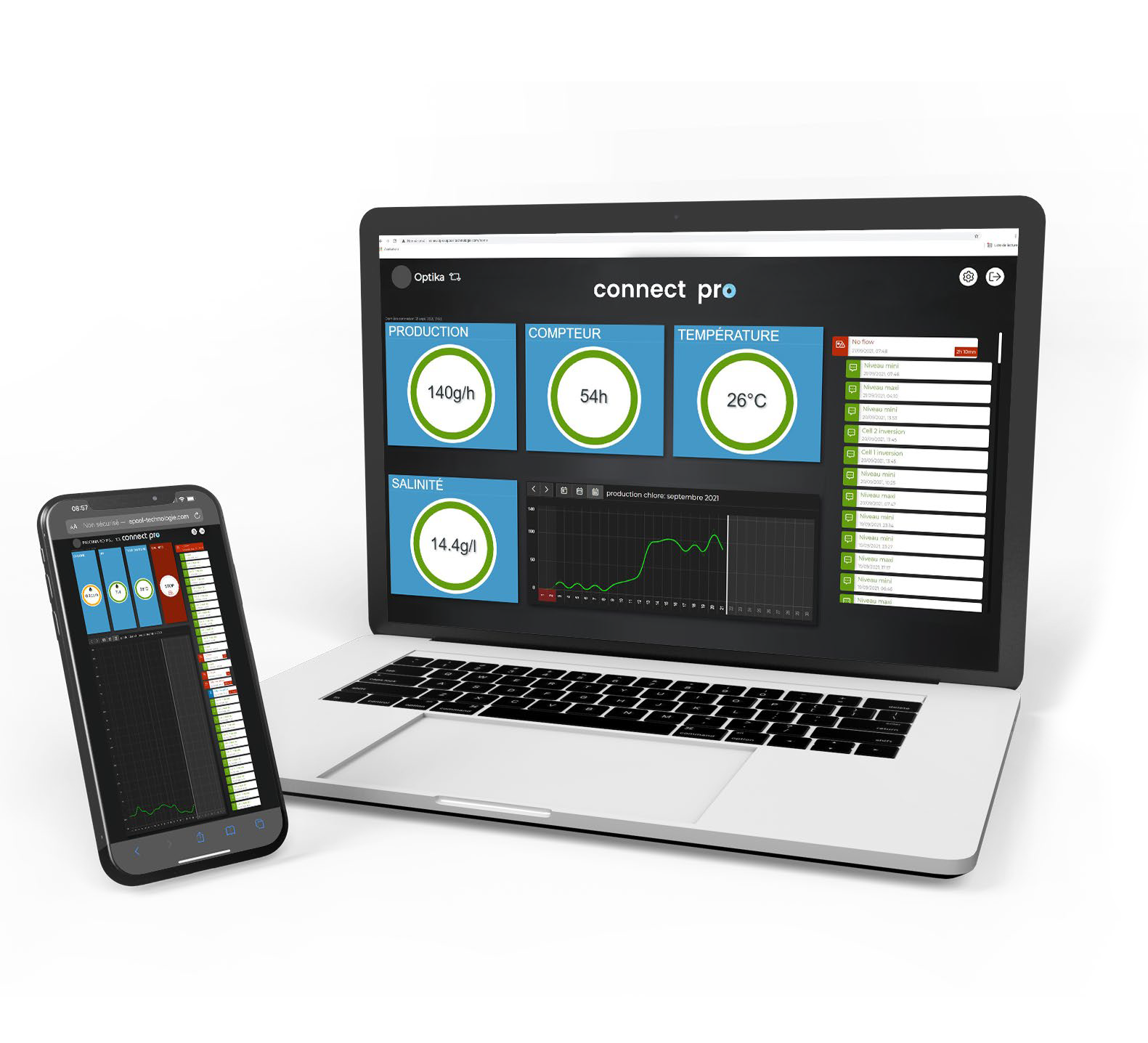
Physical RJ45 Ethernet connection to access all equipment operating data via the Connect Pro platform (included as standard) :
. Production time
. Sodium hypochlorite solution temperature
. Events
. Alarms
. Graphs
. Production curves (daily, weekly, monthly)
GSM Connection : A dedicated slot for a SIM (not supplied) is provided in the control box.
The user can assign up to 3 telephone numbers to receive any alarms detected by the system by text messages.
Keep an eye on your chlorine production !
IPOQLOR® IS THE IDEAL SOLUTION TO THESE PROBLEMS IN THE FIELS !
REAL-TIME VIEW OF
YOUR DEVICE’S VARIOUS
parameters
HISTORY
of data and alarms
–
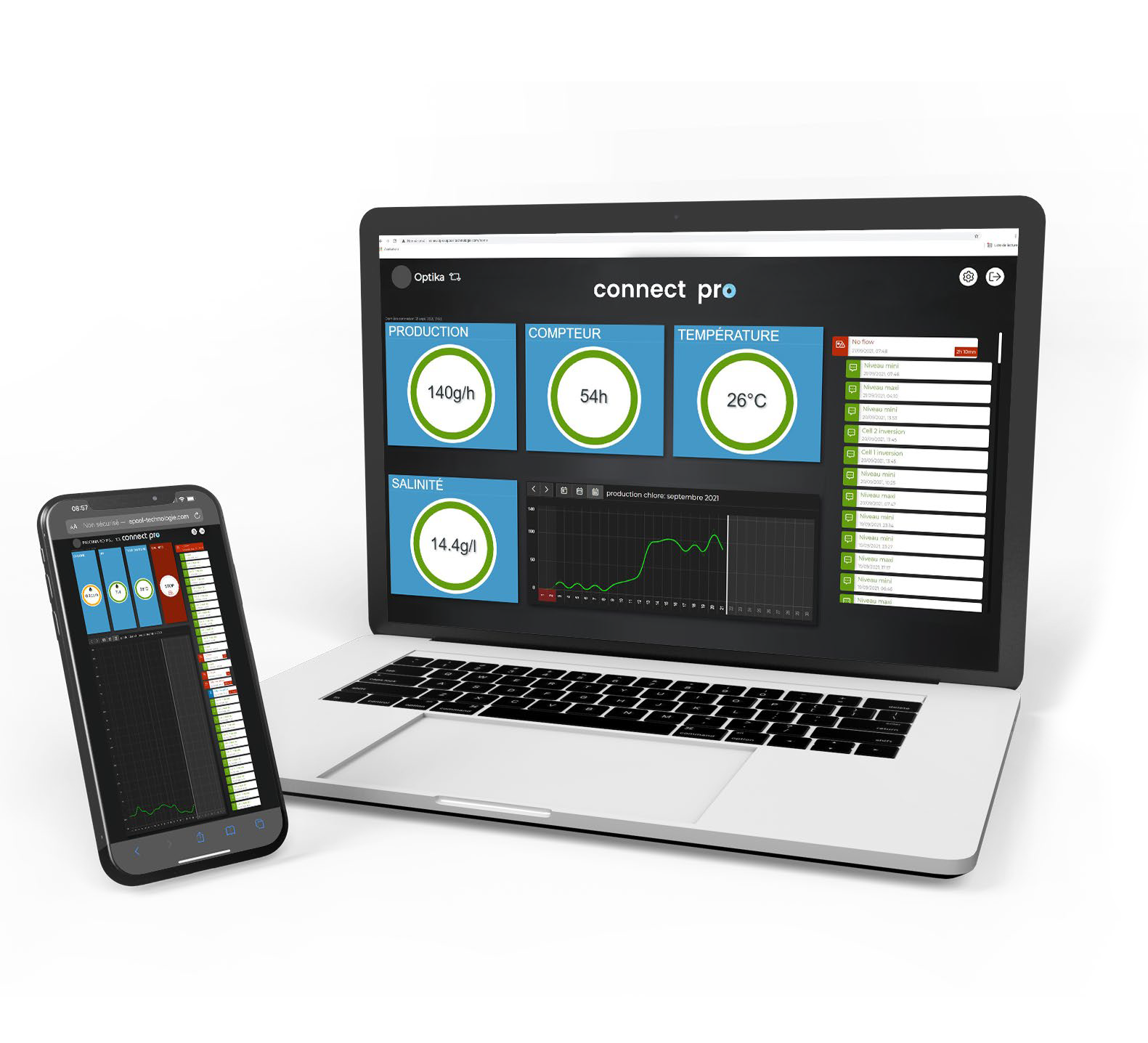
Physical RJ45 Ethernet connection to access all equipment operating data via the Connect Pro platform (included as standard) :
Production time, Sodium hypochlorite solution temperature, Events, Alarms, Graphs, Production curves (daily, weekly, monthly)
GSM Connection : A dedicated slot for a SIM (not supplied) is provided in the control box.
The user can assign up to 3 telephone numbers to receive any alarms detected by the system by text messages.
Keep an eye
on your chlorine production !
iPOQLOR® IS THE IDEAL SOLUTION TO THESE PROBLEMS IN THE FIELS !
REAL-TIME VIEW OF YOUR
DEVICE’S VARIOUS
parameters
HISTORY
of data and alarms
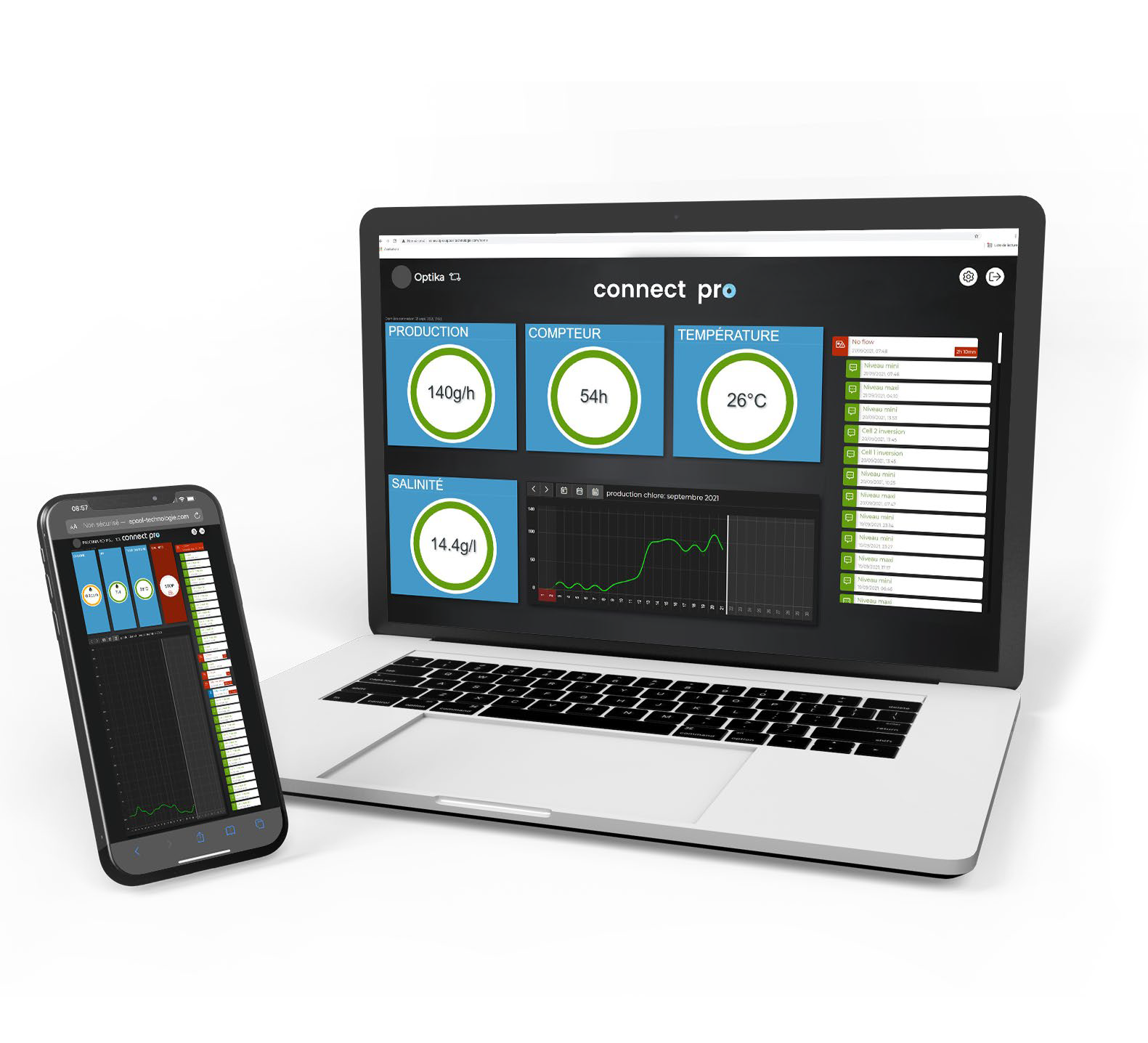
Physical RJ45 Ethernet connection to access all equipment operating data via the Connect Pro platform (included as standard) :
Production time, Sodium hypochlorite solution temperature, Events, Alarms, Graphs, Production curves (daily, weekly, monthly)
GSM Connection : A dedicated slot for a SIM (not supplied) is provided in the control box.
The user can assign up to 3 telephone numbers to receive any alarms detected by the system by text messages.
Technical specifications
iPOQLOR® range
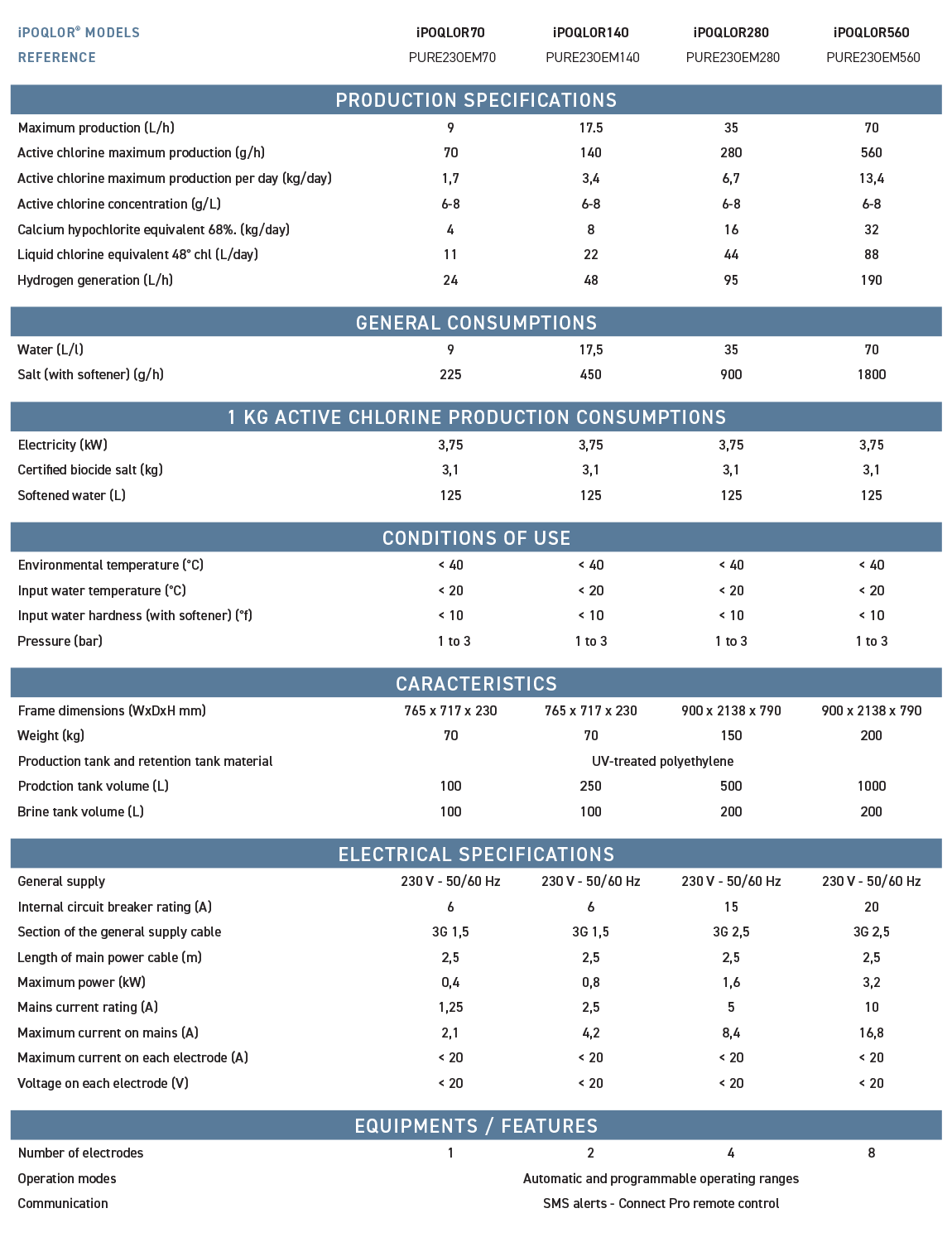
Technical specifications
iPOQLOR® range
iPOQLOR models |
iPOQLOR70 PURE22OEM70 |
iPOQLOR140 PURE22OEM140 |
iPOQLOR280 PURE22OEM280 |
---|---|---|---|
Maximum production (L/h) | 9 | 17.5 | 35 |
Active chlorine maximum production (g/h) | 70 | 140 | 280 |
Active chlorine maximum production per day (kg/day) | 1.7 | 3.4 | 6.7 |
Active chlorine concentration (g/L) | 6-8 | 6-8 | 6-8 |
Calcium hypochlorite equivalent 68 % (kg/day) | 2.5 | 5 | 10 |
Liquid chlorine equivalent 48° chl (L/day) | 11 | 22 | 44 |
Hydrogen generation (L/h) | 24 | 48 | 95 |
GENERAL CONSUMPTIONS | |||
Water (L/l) | 9 | 17.5 | 35 |
Salt (with softener) (g/h) | 225 | 450 | 900 |
1 KG ACTIVE CHLORINE PRODUCTION CONSUMPTIONS | |||
Electricity (kW) | 3.5 | 3.5 | 3.5 |
Certified biocide salt (kg) | 3.1 | 3.1 | 3.1 |
Softened water (L) | 125 | 125 | 125 |
CONDITIONS OF USE | |||
Environmental temperature (°C) | < 40 | < 40 | < 40 |
Input water temperature (°C) | < 20 | < 20 | < 20 |
Input water hardness (with softener) (°f) | < 10 | < 10 | < 10 |
Pressure (bar) | 1 à 3 | 1 à 3 | 1 à 3 |
CARACTERISTICS | |||
Frame dimensions (WxDxH mm) | 765 x 717 x 230 | 765 x 717 x 230 | 765 x 2050 x 655 |
Weight (kg) | 70 | 70 | 150 |
Production tank and retention tank material | UV-treated polyethylene | UV-treated polyethylene | UV-treated polyethylene |
Prodction tank volume (L) | 100 | 100 | 250 |
Brine tank volume (L) | 100 | 100 | 200 |
Softener resin volume (L) | 4 | 4 | 15 |
ELECTRICAL SPECIFICATIONS | |||
General supply | 230 V – 50/60 Hz | 230 V – 50/60 Hz | 230 V – 50/60 Hz |
Internal circuit breaker rating (A) | 6 | 6 | 12 |
Section of the general supply cable | 3G 1,5 | 3G 1,5 | 3G 2,5 |
Length of main power cable (m) | 2.5 | 2.5 | 2.5 |
Maximum power (kW) | 0.4 | 0.8 | 1.6 |
Mains current rating (A) | 1.25 | 2.5 | 5 |
Maximum current on mains (A) | 2,1 | 4.2 | 8.4 |
Maximum current on each electrode (A) | < 20 | < 20 | < 20 |
Voltage on each electrode (V) | < 20 | < 20 | < 20 |
EQUIPMENTS / FEATURES | |||
Number of electrodes | 1 | 2 | 4 |
Operation modes | Automatic and programmable operating ranges | Automatic and programmable operating ranges | Automatic and programmable operating ranges |
Communication | SMS alerts – Connect Pro remote control | SMS alerts – Connect Pro remote control | SMS alerts – Connect Pro remote control |